Filament Winding — Important Parameters
Composites are mostly used where conventional parts needed a beneficial replacement. The composite industry has recognized to produce high- quality, durable and cost-effective products. One of the most popular composite manufacturing method is filament winding. The method is used in different industries from automotive to oil and gas applications.
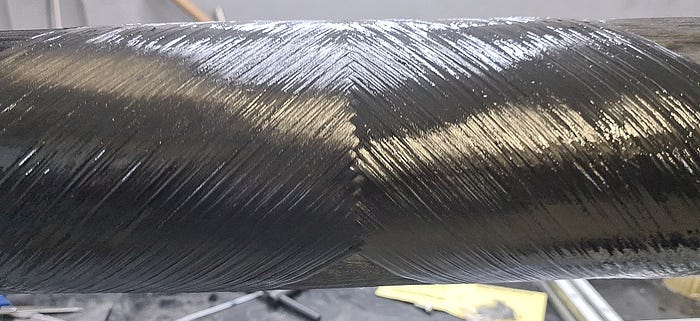
Fiber Material
When it comes to material selection, it is crucial to decide the material type to be used. Fiber types help to determine the fundamental properties of the composite products. Basically, the range of the typical properties of the fibers are roughly known, thus it is helpful to consider whether material can achieve the required properties with other process parameters in the first step of the manufacturing. The most popular fiber types used in filament winding are carbon fiber and glass fiber.
For a basic example, standard carbon fibers have an elastic modulus approximately 230 GPa. Therefore, carbon fiber can be selected if the required mechanical properties are in the range of 150-200 GPa. However, it is not easy to determine with only regarding to the fiber types. As with the definition of the composite material, the mechanical properties are determined by the composition of the process parameters.
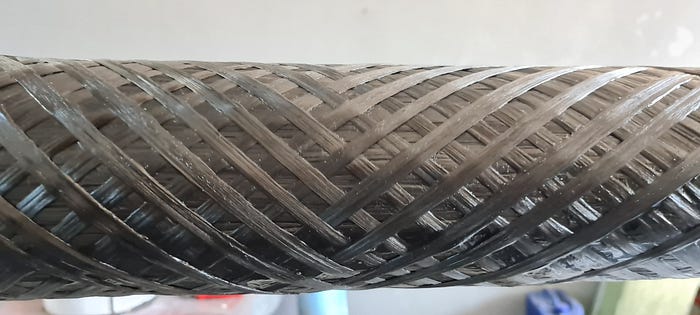
Resin
The one that must be taken into account for the second step is the selection of the resin. After the selection of the fiber type, the resin must be compatible and convenient for the fiber in order to achieve the required specific properties. The most popular resin types used in filament winding are polyester and epoxy resins.
Considering the wet winding, composite parts are cured in the oven to gain resin properties and become a composite material after the winding process. Depending on the resin type and resin chemical, composite parts acquire desired properties with specific curing temperatures and processes. Therefore, resin affects the overall performance of the composite part and must be selected carefully.
Orientations
Unlike isotropic materials such as steel, aluminium; fibers have different characteristics and mechanical properties in different directions. It is called orthotropic material. Fibers have a strong tensile strength in the unidirectional directions. Filament winding enables to use of these characteristics of the fibers by placing them in the desired locations to correspond required performance.

Fibers oriented on the mandrel at the angle of 45°, also called helical winding is used to strengthen the torque performance of the part because of the directions. It is mostly used for transmission parts or pipes. Another method is hoop winding (90°), also known as circumferential winding. Hoop winding mostly used to gain durability and overall stiffness in the parts.

Maximum tensile properties reach maximum in the longitudinal direction of the fibers. To ensure the unidirectional winding with filament special mechanisms or extra axes can be used in the industry. Therefore, fibres can reach maximum capable performance with longitudinal winding on the mandrel.